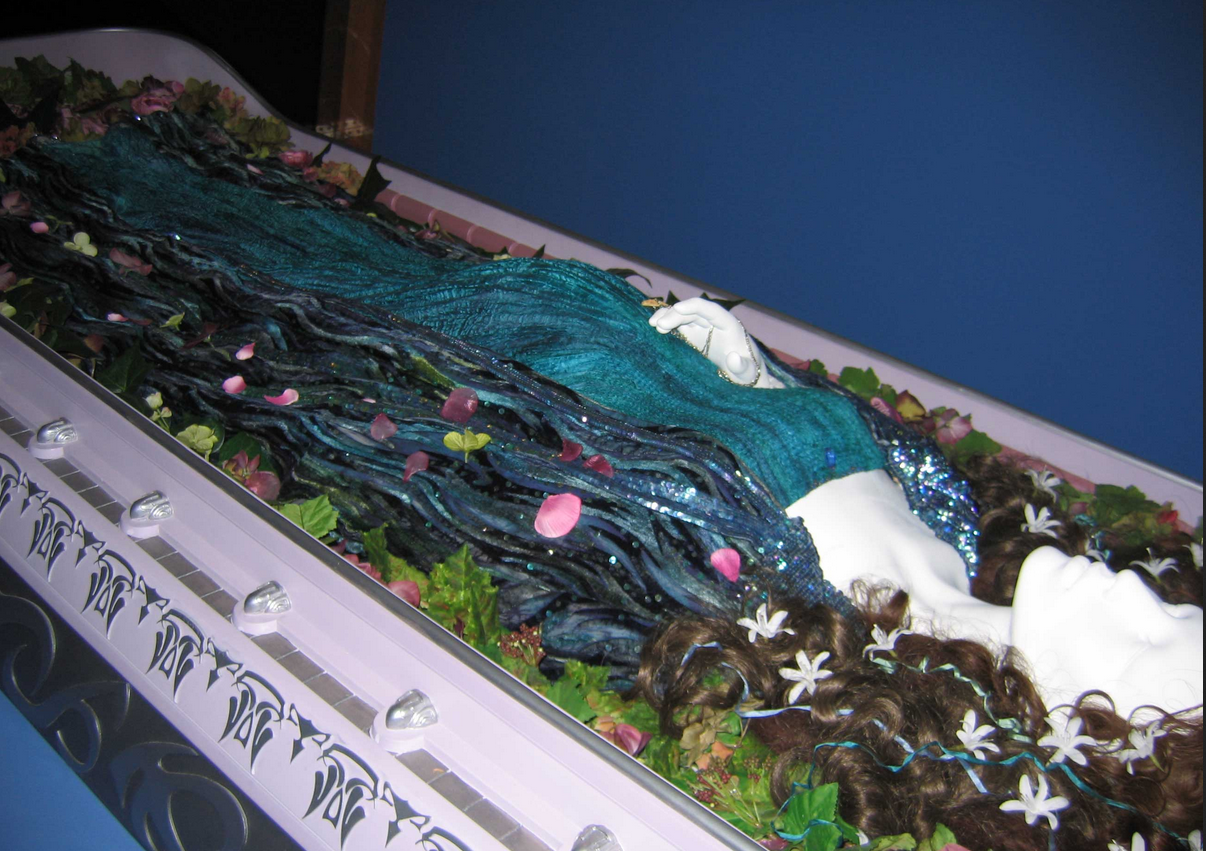
Remember my Padmé funeral cape? This one?
Well, in the tradition of redoing things a thousand time until they’re perfect, I am updating the costume. Not all of it, just the cape.
Why?
Because the original gown was made to be worn in the coffin, while you usually wear the dress standing and walking, and you’re not enclosed in a frame.
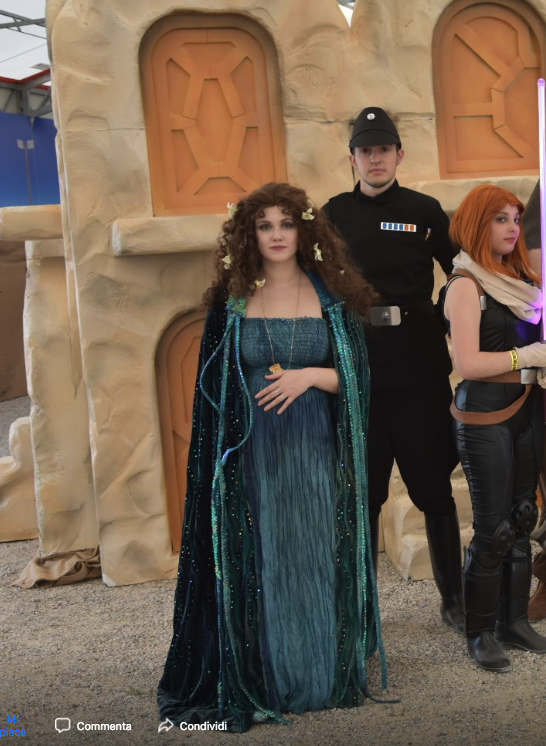
So the final effect of the floor-length cape is that of a column of water.
But the original concept is that of making Padmé look like she’s drowning, Ophelia style. The idea is that she’s going back to the waters of the lake, where she’s been the happiest she’s ever been.
So what’s the point of having a column of water? Doesn’t work.
Then, there’s the matter of the train. All her formal gowns have trains. So when you stand in an accurate replica of the cape used in the movie it is right, but it looks completely off.
So I chose to go with something more cohesive with the whole concept and the character as well.
That’s why I chose to get twice the fabric and start working.
I cut the velvet and I ombré dyed it, darker at the bottom, because I want it to be like the deepest water, at the bottom of the train.
The next step is painting, and then the devoré, which wasn’t there in the last I did, but I am positive there is in the original.
Devoré or burnout is a technique that allows you to get rid of part of the fibers that make a fabric. You can use it to make some part of silk chiffon opaque and sheer, or to get rid of the pile from silk-viscose velvet.
What’s silk-viscose velvet? The “silk velvet” you can find in stores nowadays is 99% silk-viscose velvet. There’s a base fabric, very flowy, on which the pile is woven. The base fabric is silk chiffon, while the pile is viscose.
The devoré process consists in applying a paste (the commercial one is called Fiberetch), activating it with heat, and then removing the pile, in my case. It’s a specific chemical to work on cellulose fibers (viscose is a cellulose fiber, as linen and cotton, while silk, as wool, is a protein fiber). Being the back silk, it doesn’t get damaged (or at least it should not).
Apparently no one is shipping that thing to Italy, so after a long time of scouting online I have found a recipe. I have tested it and changed it until it worked at its best, but I won’t share the recipe, as I’m not the proper person to give you dangerous chemical recipes with the risk of having someone do something bad because of it. So, if you want to try, get the commercial one
I tested quite a lot. I already tried it three years ago, but didn’t manage to get a nice result and stopped. Now I tried again. The technique isn’t perfect yet.
You basically want to spread the paste with a brush, dry it, and then heat it to 140°c. Then you rub the pile away and clean it with water. Easy peasy?
It’s not. It’s a nightmere. Silk starts to change color in a similar temperature range. You have to heat the paste until it gets brown-ish, but the silk around it reacts first sometimes. I’ve tried with the iron to press clothing, with a heat gun. In both ways the paste hardens and becomes corrugated, and some parts tend to burn while others don’t react. If you insist, you get holes in the silk too.
I tried getting the paste even and thin, or heating it slowly, but it’s a bit of a mess.
Now I am waiting o get back to the mountains to attach the sequins.